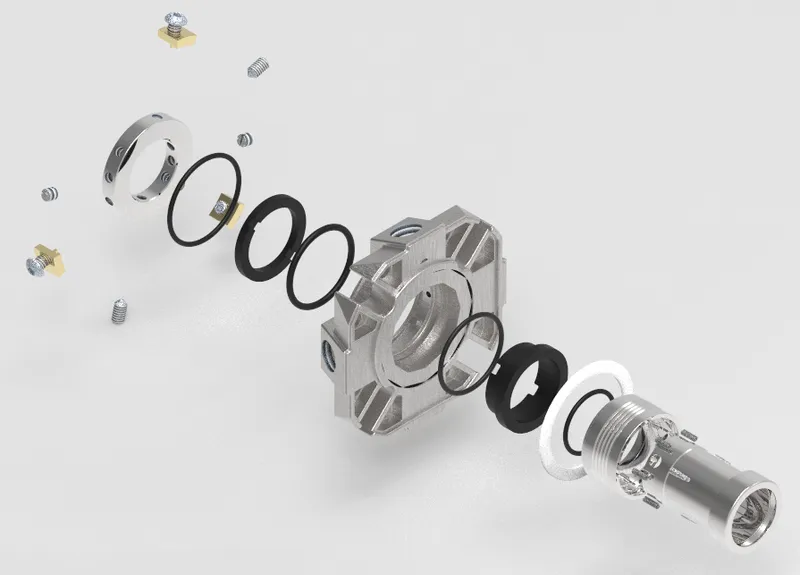
Mechanical seals are vital, integral components across all industry sectors, playing a pivotal role in preventing fluid leakage and ensuring the seamless operation of rotating equipment such as pumps, including centrifugal pumps, rotary lobe pumps, diaphragm pumps, gear pumps and compressors.
In this comprehensive guide, we delve into the intricacies of mechanical seals, exploring their types, applications, advantages, and crucial aspects of installation and maintenance.
The article will describe how mechanical seals work and explore the critical aspects which differentiate good performance from poor or inadequate performance.
Additionally, we'll uncover how Reliability Engineering services and products can significantly benefit your operations.
Centrifugal pumps are the most common type of pump used in industry since they are suitable for most types of process media, specifically used for handling water and oils and they are relatively easy to manufacture.
There are many companies who manufacture centrifugal pumps including ITT Gould's, Flowserve, KSB, Grundfos, and Kirloskar. Traditionally, pumps were sealed with gland packing, lip seals and other different types such as ineffective component sealing devices with unbalanced seal faces, which create equipment wear and/or excessive heat generation leading to premature equipment failure.
Reliability Engineering offer innovative mechanical seal solutions, seal support systems and bearing seals for all types of rotating equipment and centrifugal pumps.
Before delving into the complexities of mechanical seals, let's grasp the fundamentals of their construction. A typical mechanical seal comprises two main components: the stationary element and the rotating element. The stationary element is usually affixed to the pump housing, while the rotating element is connected to the pump shaft. Working in tandem, these elements form a barrier that prevents the escape of fluid or gas from the pump or compressor.
Moreover, mechanical seals feature a sealing face where the stationary and rotating elements make contact. This critical sealing face is crafted from durable materials such as ceramic, carbon, or silicon carbide, ensuring resilience in the demanding conditions of industrial operations.
Mechanical seals come in various seal types, each tailored to meet specific operational requirements. Although mechanical seals are installed in a wide range of equipment, the most common are pump seals. The types of pump seal includes:
Examples of the most common mechanical seals for pumps, are Single and Double cartridge type seals as shown below;
Mechanical seals incorporate two main components: a stationary part (often referred to as the seal housing or gland) and a rotating part (referred to as the seal head or rotating face). Contained in the rotating part is one or more rotating mechanical seal faces. Contained in the stationary part is one or more stationary mechanical seal faces. In its basic form, the mechanical seal is formed between the counter-rotational friction seal faces, which prevent process fluid escaping the pump or item of rotating equipment.
Unlike mechanical lip seals which use rapid wearing elastomeric, rubber and polymer type materials, the counter-rotational mechanical seal faces are made from durable materials such as carbon, tungsten carbon and silicon carbide. When supported with secondary seal assemblies such as oring's and gaskets, the mechanical seal creates a comprehensive sealing device with prolongs rotating equipment longevity when applied correctly. ...... and that's the trick. Applying the right mechanical seal solution to the right application is the secret to sealing success.
A good analogy is a formula one race car and a jeep. The formula one race car comprises of excellent technology for high speed, flat ground conditions. If you take a formula one car on rough, rocky and hilly terrain with wet sludgy ground, it will NOT perform. That's when jeep technology comes into play. Mechanical seal technology is no different. You can misapply a mechanical seal in the same way you can misapply a formula one car. Aligning yourself with an experienced and reputable mechanical seal supplier, such as Reliability Engineering, who understands seal types and technology, is one way to help avoid misapplication.
Between the counter-rotational seal faces of a mechanical seal is something called a 'fluid film'. The fluid film helps to cool and lubricate the counter-rotational faces, helping to prolong seal face. If the fluid film is too large, the mechanical seal will leak. If the fluid film is too small, the mechanical seal will overheat and burn-out. Therefore the essential element of all mechanical seals, to to maintain the right fluid-film conditions for the application.
There are many ways to improve the fluid film in a mechanical seal. Hydraulically balanced seals is one such method, along with Plan 53 systems.
Click here to learn more about mechanical seal fluid film and how mechanical seals work.
The versatility of mechanical seals makes them indispensable across various industries and types of rotating equipment which typically contain a power transmitting shaft. Sealing to prevent leakage is a major driving factor to use mechanical seals over gland packing. Some applications include:
The widespread use of mechanical seals extends across diverse industries, contributes to the smooth operation of critical processes in sectors such as:
As a leading provider of mechanical seal solutions, we proudly introduce our comprehensive range of services, including the innovative "Reiuptime-Equipment Healthcare" initiative. This customer equipment healthcare program, operated by Reliability, is specifically tailored for channel supply customer contracts and partnerships. "Reiuptime" focuses on ensuring the health and longevity of equipment through proactive maintenance and support.
Our commitment to excellence in services, spanning design, manufacturing, assembly, and customer support, is evident in the "Reiuptime-Equipment Healthcare" initiative. With a focus on innovation and customer satisfaction, we aim to be your preferred partner in mechanical seal solutions.
In addition to our comprehensive services, we take pride in offering a diverse range of high-quality mechanical seal products:
Check out out product range here for detailed information.
In conclusion, understanding the intricacies of mechanical seals is imperative for industries relying on efficient and leak-free machinery. The diverse types and applications of mechanical seals make them indispensable components in various sectors, ensuring the smooth operation of critical processes. As a leading provider of mechanical seal solutions, our commitment to quality services and products is aimed at helping our clients achieve optimal performance, reliability, and longevity in their mechanical seal applications.
Whether you operate in the oil and gas, chemical, pharmaceutical, water treatment, or power generation industry, our team is dedicated to providing customised solutions to meet your specific needs. Contact us today to explore how our expertise can enhance the efficiency and reliability of your mechanical seal applications.