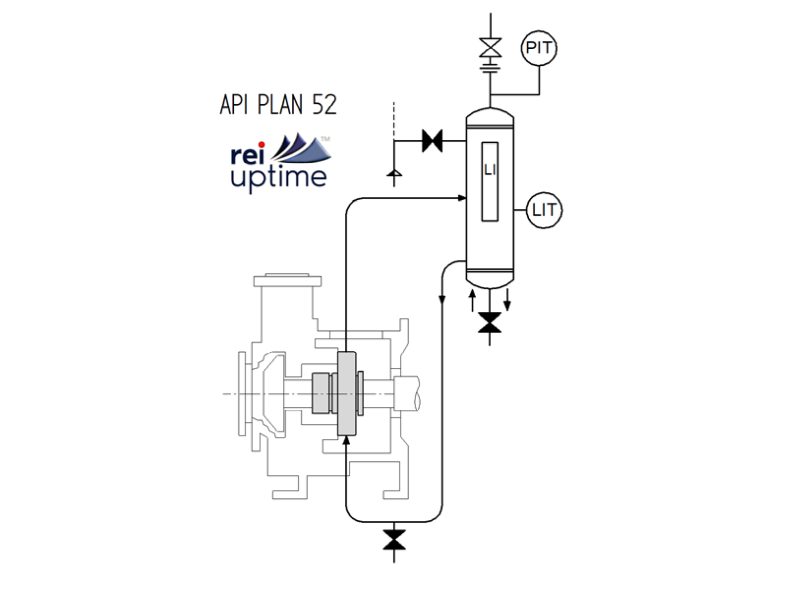
Mechanical seals are only as good as the environment in which they operate. That environment, whether clean or contaminated, pressurised or dry, is determined largely by the seal support system in place. These systems are not just accessories; they are vital components that influence the efficiency, durability, and safety of the entire sealing solution.
At Reliability Engineering Industries, we've seen how well-designed and properly maintained seal support systems can dramatically reduce downtime, prevent failure, and extend equipment life.
A seal support system is an auxiliary system that maintains specific environmental conditions around the seal. It can provide:
These functions become crucial when operating in demanding conditions such as high pressures, toxic environments, or abrasive slurries. Without effective support, even the most advanced seal design can fail prematurely.
The American Petroleum Institute (API) standard 682 outlines a series of Seal Support Plans, structured methods to manage the seal environment. Among these, API Plans 52, 53, and 54 are the most commonly deployed in dual seal configurations.
Let’s break them down:
Used with unpressurised dual seals, this plan relies on a buffer fluid circulating between the seals. The main functions include:
Plan 52 systems often use an external reservoir and rely on natural convection or forced circulation. A level or pressure switch can help detect inner seal failure early by observing buffer fluid loss.
Risk Without It:
Without buffer fluid, the outer seal may run dry and wear rapidly, especially if the inner seal fails.
Our Advice:
Reliability Engineering Industries recommends using Plan 52 for non-hazardous services where internal leakage is tolerable but controlled seal chamber conditions are needed.
Plan 53 is used with pressurised dual seals. The system maintains a barrier fluid at a pressure higher than the process fluid to:
There are sub-types (Plan 53A, 53B, 53C), differing in how the barrier fluid pressure is maintained, ranging from bladder accumulators to pressurised reservoirs.
Risk Without It:
In hazardous or aggressive services, failure to maintain pressurisation can lead to leakage of harmful fluids, safety incidents, and seal destruction.
Our Advice:
When zero-emission performance is critical, Reliability Engineering Industries configures Plan 53 systems with smart pressure control and emergency alarms.
This plan uses an external pressurised system to circulate barrier fluid independently of the process pump. It’s suitable for:
Risk Without It:
Plan 54 is often the only way to deliver adequate cooling and pressure control in complex or hazardous processes.
Our Advice:
We design and supply custom-built Plan 54 skids at Reliability Engineering Industries to integrate with your plant’s DCS, ensuring full system monitoring and control.
The heart of every seal support system is its fluid, either barrier (pressurised) or buffer (unpressurised). The choice of fluid and its condition has a profound effect on seal performance.
Common Fluids Include:
Fluid TypeUse CaseMineral oilsGeneral-purpose lubricationWater-glycol mixesFire-safe environmentsSynthetic oilsHigh-temperature or reactive systemsProcess-compatible fluidsWhere leakage into the process must not contaminate it
Reliability Engineering Industries ensures all support systems include fluid filtration, temperature control, and fluid monitoring instruments to protect against contamination and degradation.
While installing a seal support system is crucial, it must also be managed proactively. Based on our experience supporting industrial clients globally, here’s how to get the best from your system:
At Reliability Engineering Industries, our integrated approach to seal and support system design ensures performance, safety, and longevity. We offer:
Mechanical seal reliability isn’t just about the seal itself, it’s about the complete system. At Reliability Engineering Industries, we go beyond manufacturing seals. We engineer total solutions with robust seal support systems tailored to your unique application.
Whether you need to upgrade an existing Plan 53 system or want to implement a fully automated Plan 54 skid, our team has the technical depth and application knowledge to support your success contact us today.