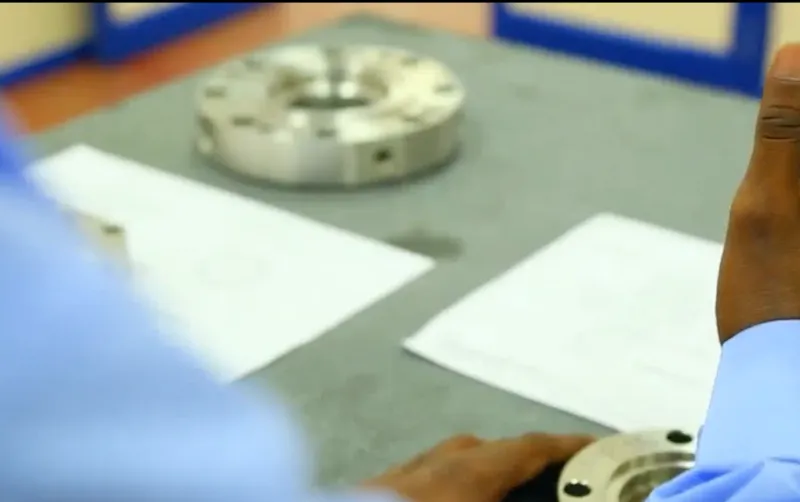
In critical industries such as oil & gas, chemical processing, and power generation, mechanical seals are unsung heroes. These components ensure safe and leak-free operation in rotating equipment like pumps and mixers. When they fail, consequences can be severe, ranging from unplanned shutdowns to environmental incidents. At Reliability Engineering Industries, we’ve worked with countless operations facing mechanical seal issues. Our team has identified recurring failure patterns and developed time-tested strategies to prevent them.
Dry running occurs when the seal faces operate without adequate lubrication. Since most mechanical seals depend on a fluid film between the faces to reduce heat and friction, the absence of it causes overheating, rapid wear, and ultimately seal failure. This situation often results from:
Prevention Tip:
Always ensure the pump is fully primed and the system is vented before starting. Install flow detection or pressure sensors to monitor seal chamber conditions. Reliability Engineering Industries recommends seal support systems like flush plans to guarantee consistent lubrication.
Misalignment between the pump shaft and driver coupling can put lateral stress on the seal faces. It leads to uneven wear, cracked faces, and distorted seal components. This issue can stem from:
Prevention Tip:
Implement routine shaft alignment checks using laser tools. Precision installation is key, Reliability Engineering Industries provides training and alignment services to support field teams in achieving accurate fits.
Seal faces are designed to run with a clean film of fluid. But solid particles, corrosion debris, or chemical precipitates can get trapped between faces, leading to scoring, blistering, or pitting. Contamination often arises from:
Prevention Tip:
Upgrade filtration systems and implement a consistent fluid monitoring programme. Reliability Engineering Industries offers corrosion-resistant seal designs and custom materials that tolerate harsher environments.
Even the best seals will fail if not installed correctly. Issues such as incorrect torque, misplacement of O-rings, or contamination during assembly are far too common.
Prevention Tip:
Follow manufacturer guidelines meticulously. Where possible, involve trained personnel. At Reliability Engineering Industries, our field service team performs onsite installation audits to reduce first-time installation errors.
Excessive vibration accelerates wear, causes micro-fractures, and misaligns seal components. It often indicates underlying problems such as:
Prevention Tip:
Diagnose and address the root cause of vibration promptly. Seal reliability improves significantly when mechanical health is monitored. We often install vibration sensors and provide condition monitoring services to stay ahead of failures.
A sudden change in temperature can cause seal materials to crack, warp or lose elasticity, particularly if incompatible materials are used. This can happen during:
Prevention Tip:
Use seals with materials compatible with thermal cycling. Our engineers at Reliability Engineering Industries recommend composite seal faces and elastomers that withstand high-temperature applications.
When seals are exposed to chemicals outside their design specifications, the damage is inevitable. Swelling, cracking, and hardening of seal elements signal material degradation.
Prevention Tip:
Conduct compatibility checks for all process fluids. We supply chemical-resistant materials like PTFE, FFKM, and Hastelloy, specifically tailored for harsh chemical environments.
The key to improving mechanical seal life is not just in better design, but in smarter maintenance. Here are strategies Reliability Engineering Industries encourages clients to adopt:
Mechanical seals don’t fail randomly. With informed design choices, proper maintenance, and precision installation, they can last significantly longer. At Reliability Engineering Industries, our holistic approach includes:
Each seal we produce undergoes stringent checks to ensure performance under your real-world conditions, not just in the lab. We also assist clients in retrofitting existing systems with upgraded sealing solutions that extend operational life.
At Reliability Engineering Industries, we understand the operational and financial consequences of seal failures. That’s why we work closely with clients to design, maintain, and support mechanical seal systems that stand the test of time.
Whether you are struggling with premature failures or simply looking to upgrade your sealing technology, our team is here to help. Get in touch today to learn how we can assist your operation.