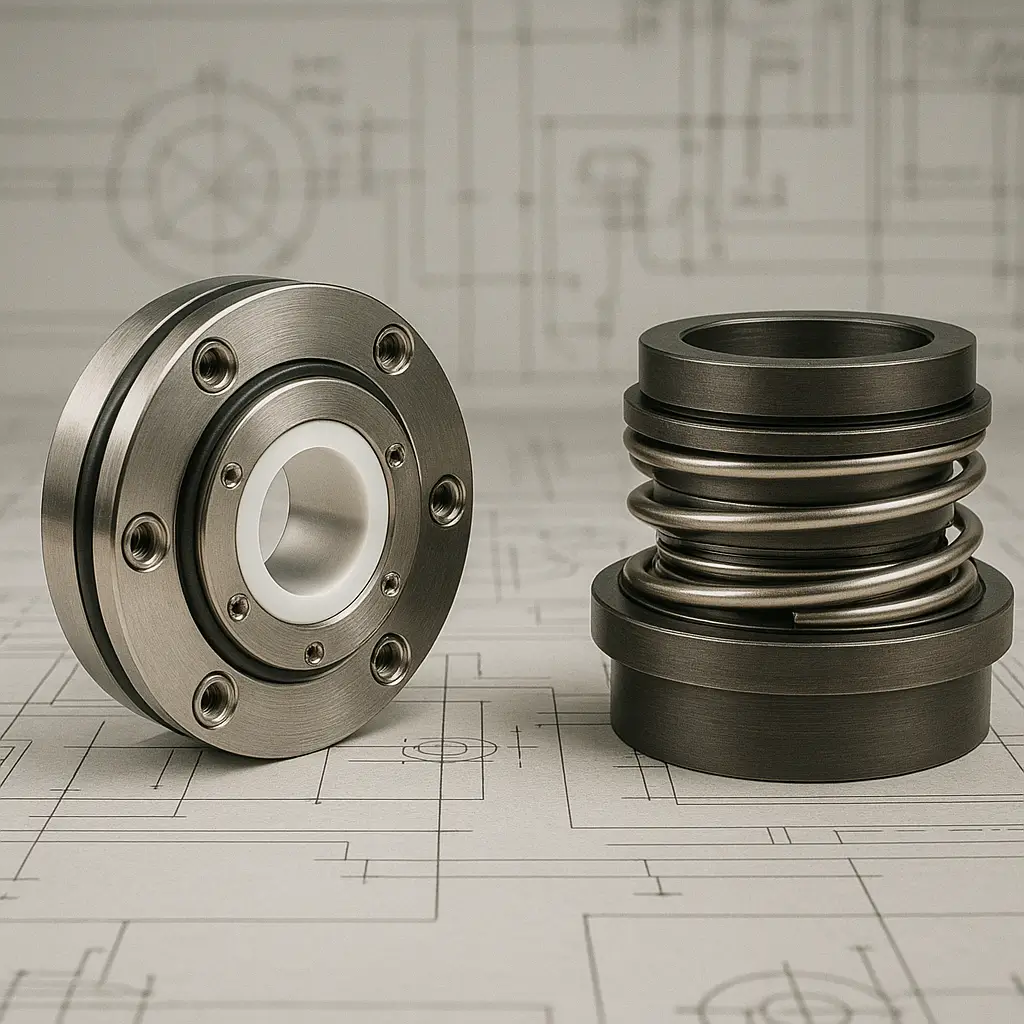
When it comes to sealing technology in rotating equipment, the choice between dry gas seals and wet seals has a significant impact on operational efficiency, cost, and reliability. Reliability Engineering Industries provides expertise and solutions in both technologies, supporting a wide range of industrial applications with seals tailored to specific operational demands.
Understanding the differences between dry gas seals and wet seals helps operators make informed decisions about which system best suits their environment, performance requirements, and maintenance objectives.
Dry gas seals operate without the need for a liquid barrier. Instead, they use a thin gas film, typically nitrogen, to create a non-contacting seal between rotating and stationary components. These seals are widely used in compressors and high-speed machinery, where minimal friction and low wear are essential.
Reliability Engineering Industries offers dry gas seals designed for high-performance environments, providing efficient sealing while reducing energy loss and contamination risks.
Wet seals, also known as mechanical seals with a liquid barrier, use fluid—often oil or water-based—to create a seal. The liquid serves to lubricate the seal faces and dissipate heat generated by friction. Wet seals are commonly used in pumps, mixers, and agitators where operating conditions involve lower speeds and higher fluid contact.
Reliability Engineering Industries manufactures wet seals with precision, ensuring reliable operation and long service life in demanding industrial settings.
The decision between dry gas seals and wet seals depends on several factors, including operating pressure, temperature, fluid type, environmental regulations, and cost considerations.
Reliability Engineering Industries works closely with clients to assess their specific needs and recommend the most suitable sealing technology. With expertise in both dry gas and wet seals, the company ensures that each solution delivers long-term value, efficiency, and operational reliability.
The team at Reliability Engineering Industries uses advanced design and testing methods to ensure that every seal meets the highest standards of performance and safety. Their in-depth knowledge of industry requirements makes them a trusted partner for sealing solutions across sectors.
Need help determining whether dry gas seals or wet seals are right for your application? Contact Reliability Engineering Industries today for expert guidance and reliable sealing solutions tailored to your operational needs.