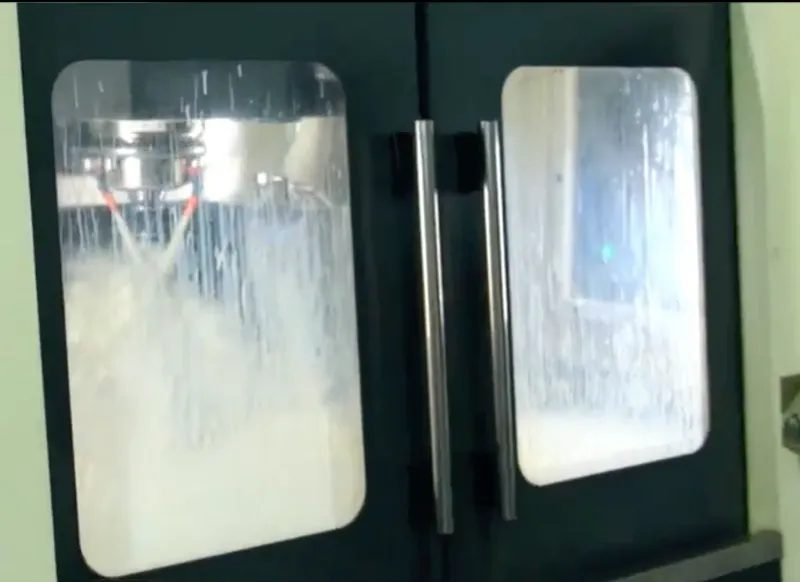
Operating in extreme conditions demands more from mechanical seals than standard applications. High temperatures, intense pressures, and aggressive chemicals can challenge even the most robust equipment. Reliability Engineering Industries specialises in designing seals that perform reliably under these demanding conditions, ensuring safety, efficiency, and longevity.
Industrial environments such as chemical processing, power generation, and oil & gas often involve high temperatures and pressures that can cause conventional seals to fail. Reliability Engineering Industries offers mechanical seals engineered to withstand temperatures exceeding 400°C and pressures beyond 100 bar, depending on the specific application.
These seals are used in:
Each seal design is tailored to ensure minimal deformation and optimal sealing performance, even as materials expand and contract under thermal stress.
The performance of a mechanical seal in extreme conditions is closely tied to the materials used in its construction. Reliability Engineering Industries places significant emphasis on selecting materials that can handle the unique stresses of high-temperature and high-pressure environments.
Commonly used materials include:
Elastomers such as Viton, EPDM, and Kalrez are chosen based on their ability to maintain elasticity and sealing capability at elevated temperatures. Material compatibility with process fluids is also rigorously evaluated to prevent chemical degradation over time.
Reliability Engineering Industries continually invests in innovation to ensure that seals not only survive but thrive in the harshest environments. Key innovations include:
These innovations are the result of continuous research and development, a core focus at Reliability Engineering Industries, where each seal is tested rigorously to meet exacting industry standards.
By offering solutions specifically designed for these sectors, Reliability Engineering Industries ensures reliable operation, minimised downtime, and extended maintenance intervals.
No two applications are identical, especially in extreme environments. Reliability Engineering Industries collaborates closely with clients to develop customised seal solutions that meet their exact operational needs.
Through detailed consultation, material analysis, and precision engineering, the team ensures each seal system offers:
Clients trust Reliability Engineering Industries for their ability to translate complex sealing challenges into practical, effective solutions.
Contact Reliability Engineering Industries Today
Need a sealing solution for extreme conditions? Contact Reliability Engineering Industries to discuss your high-temperature and high-pressure application requirements. Our experts are ready to provide custom-engineered seals designed for performance and reliability under the toughest conditions.