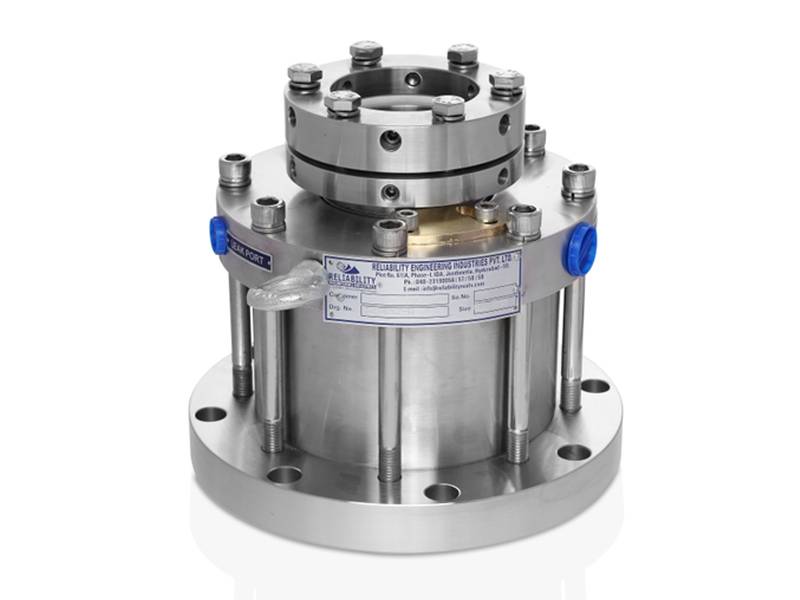
Industrial pumps are at the heart of critical processes in sectors such as chemicals, oil & gas, and pharmaceuticals. To ensure maximum reliability, especially in hazardous or high-risk environments, many operators turn to dual mechanical seals. Reliability Engineering Industries provides high-performance dual seal systems designed to enhance operational safety, prevent leakage, and support compliance with stringent industry standards.
Single mechanical seals can be effective in many applications, but in hazardous environments, the stakes are higher. Fluid leakage, even in small amounts, can lead to environmental contamination, safety hazards, or damage to expensive equipment. Dual mechanical seals, consisting of two sets of sealing surfaces, provide an extra layer of protection by containing the process fluid within the pump and preventing leakage to the atmosphere.
Reliability Engineering Industries designs dual seals specifically for:
The additional sealing barrier ensures that even if the primary seal fails, the secondary seal will continue to maintain containment, greatly reducing the risk of leaks.
Dual mechanical seals can be configured as pressurised (also known as double seals) or unpressurised (tandem seals). The choice between these two types depends on the application, safety requirements, and process conditions.
Reliability Engineering Industries supplies pressurised dual seals for applications where zero leakage is critical, ensuring complete isolation of the process medium.
Reliability Engineering Industries offers unpressurised dual seals for processes where added protection is needed but without the complexity of maintaining pressurised barrier systems.
While dual mechanical seals typically involve a higher initial investment compared to single seals, the long-term benefits often outweigh the costs, particularly in high-risk or mission-critical environments.
Reliability Engineering Industries works closely with clients to assess the cost-benefit balance for each application, ensuring the right seal choice for maximum value and performance.
Each application benefits from the increased reliability, safety, and durability that dual mechanical seals from Reliability Engineering Industries provide.
Not all dual seals are created equal. Reliability Engineering Industries custom-engineers dual mechanical seal systems to match the unique requirements of each process. With expertise in material selection, seal design, and API support systems, the team ensures that each solution delivers on both performance and value.
From the initial consultation to final implementation, clients trust Reliability Engineering Industries to provide seals that stand up to the most demanding industrial environments.
Considering dual mechanical seals for your industrial pumps? Contact Reliability Engineering Industries for expert advice, tailored sealing solutions, and support to ensure your operations run reliably and safely.