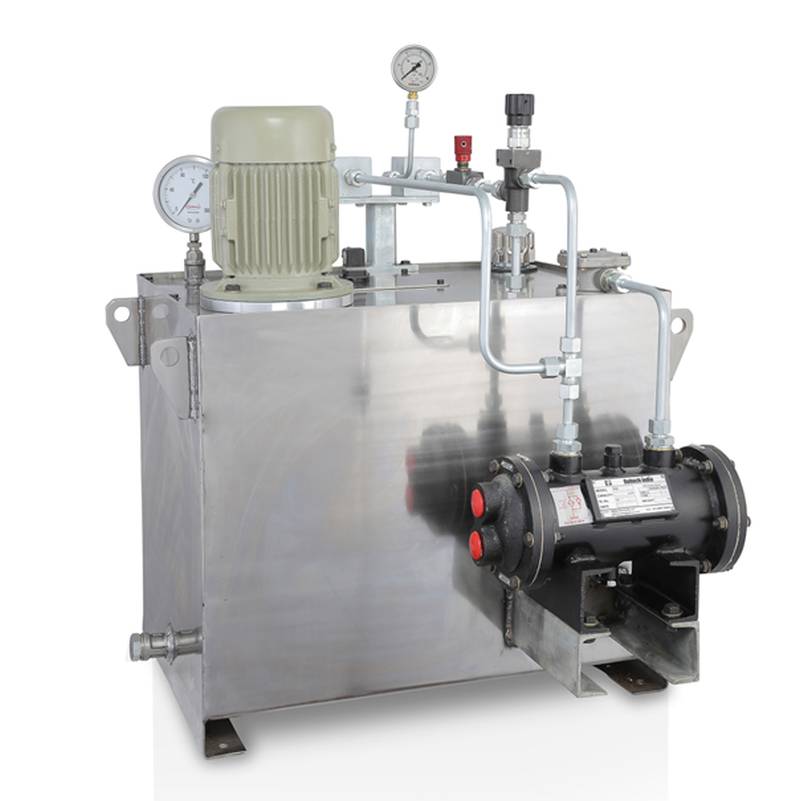
In industries where process temperatures soar well above 150°C, choosing the right mechanical seal support system becomes a defining factor in system reliability, safety, and operational efficiency. Whether operating in power generation, petrochemicals, or heavy-duty manufacturing, engineers are constantly tasked with mitigating heat-related seal failures.
High-temperature environments pose several technical challenges for mechanical seals. Excessive heat can accelerate wear, degrade lubricants, and impact seal face materials. Without proper support, seals may fail prematurely, leading to unplanned downtime, higher maintenance costs, and safety risks.
To combat this, seal support systems play a pivotal role by providing necessary lubrication, cooling, and pressure regulation. Among these systems, API Plans 52, 53, and 54 are commonly used, each with distinct advantages based on application demands.
API Plan 52 involves an unpressurised buffer fluid system. It is primarily used with dual unpressurised seals and relies on a reservoir to cool and lubricate the seal faces. While adequate for moderate temperatures and less aggressive processes, Plan 52 has limitations in high-temperature applications due to the lack of forced cooling.
Moving up the scale, API Plan 53 introduces a pressurised barrier system using either gas or liquid to protect the inner seal. It improves reliability by maintaining a higher pressure in the barrier system than the process side, which reduces leakage and thermal stress. Although more robust than Plans 52, it still may not be optimal for applications above 180°C or where consistent circulation is needed to manage heat effectively.
When temperature demands become extreme, API Plan 54 offers the most comprehensive solution. It is a custom-engineered forced circulation system that delivers continuous cooling and lubrication using a pressurised external fluid system. This design ensures maximum control over heat management, even in the harshest operating environments.
At Reliability Engineering Industries, we recommend Plan 54 System: STAN100-FCS for high-temperature processes up to 200°C. This system stands out for its advanced engineering and application-focused design.
The STAN100-FCS is a 100-litre oil forced circulation system engineered for reliability under pressure. Manufactured from 316 stainless steel, it is built to withstand high thermal loads while resisting corrosion. The unit includes a positive displacement pump that circulates oil at up to 4 L/min to maintain consistent cooling at the seal interface.
Designed for floor or skid mounting, the system incorporates a plate heat exchanger to dissipate heat efficiently, while its integrated pressure and temperature gauges provide precise operational monitoring. Optional features like ATEX certification and integral cooling coils further enhance its flexibility in demanding industrial settings.
Reliability Engineering Industries does not only supply mechanical seal systems, we offer a comprehensive support ecosystem. From design and development to repair and refurbishing, our team ensures that every system performs at peak efficiency throughout its lifecycle.
For businesses operating in sectors where uptime is non-negotiable, our assembly and testing services ensure every component meets performance standards before installation. We also provide inventory and customer service support, allowing clients to reduce lead times and plan maintenance activities without delays.
Our engineering team collaborates directly with customers to ensure that every seal support system, including the STAN100-FCS, is tailored to site-specific requirements. Whether it's adapting the hose length for remote installations or integrating additional instrumentation, we build to fit—not the other way around.
Monitoring fluid conditions is essential in any high-performance environment. That’s why the STAN100-FCS comes standard with oil level, temperature, and pressure indicators. Clients can also opt for fully instrumented versions equipped with high/low pressure switches for added protection.
Our Plan 54 solutions, particularly the STAN100-FCS, are trusted by chemical processing plants, oil and gas facilities, and refineries across India and beyond. In these sectors, equipment often runs at full capacity for extended periods. Only systems engineered for durability and performance can deliver the results clients demand, and that's what Reliability Engineering Industries is known for.
At Reliability Engineering Industries, we take pride in delivering not just equipment but confidence. Our consultative approach ensures that each client receives a solution aligned with their technical needs and operational goals.
By choosing the right seal support system for high-temperature applications, organisations protect their investments, reduce environmental risk, and ensure safe, consistent operation. And with STAN100-FCS, backed by expert service and technical insight, you're in capable hands.
Have questions about selecting the right mechanical seal support system for your high-temperature application? Contact the team at Reliability Engineering Industries today to speak with our experts and find the ideal solution tailored to your needs.